Product Types Used | Air Cannon Solutions |
---|---|
Industry | Grain Hauling and Food Processing |
Customer | Alaskan Brewing Company, Juneau, AK |
Problem

Ash accumulation issues had been forcing Alaskan Brewery Company to shut down its equipment to cool and manually clean the swirlers and collectors of its ash handler on a weekly basis. The process required an outage of 3-4 days, including as much as twelve hours of maintenance time with bottle brushes and bead blasting.
“Unlike other fuels typically used in the brewing process, dried grain also produces an extremely fine ash that readily absorbs moisture from the atmosphere,” Maintenance Supervisor Suki Patterson continued. “It tends to develop a gummy texture, so it can collect on the interior surfaces and become difficult to remove.”
Solution

The brewery contacted Martin to discuss potential solutions. After reviewing the engineering drawings, Martin suggested a sonic horn to help improve ash flow and prevent clogging in the exhaust stream of its ingenious hybrid boiler system that uses spent grain from the brewing process as fuel.
The sonic horn is a proven technology that can raise throughput and reduce blockages in a very wide range of materials, preventing dry particulate build-up to increase system efficiency and service life, while reducing downtime and maintenance. The acoustic cleaner has been widely used in the process industries, particularly in cement manufacturing. In addition to its low cost of ownership, acoustic cleaning helps avoid structural fatigue or damage.
Results

Alaskan Brewery reported an immediate improvement after installation. And now, instead of shutting down the equipment after just 25 hours of operation, the system can complete an entire brewing cycle, with little or no performance loss in 94 hours of boiler run time.
Patterson stated, “Even though brewing is not an important market for Martin Engineering, they spent a lot of time to help resolve an issue that had been a nagging problem for us. It was a very small sale — just one component — but it meant a great deal to us. They have been great to work with.”
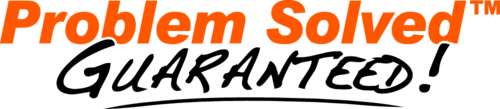
We've solved your problem somewhere before!
While your problem seems unique and frustrating, with 70+ years of solving similar problems around the world, and with the most experienced and educated people on our teams, we can assure you that we’ve “Been There, Done That.” At least close enough to know what needs to be done next and adjust for your situation.
Put Us To The Test For Free! Let Us Give You a Solution.